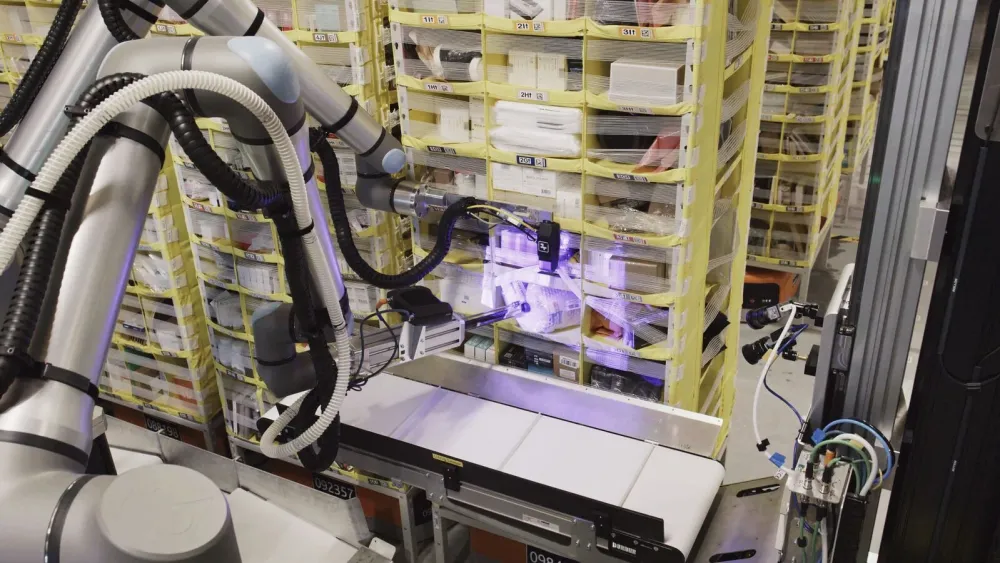
Amazon has announced that it has now deployed over 750,000 robots across its fulfillment centers and has recently introduced a new generation of robotic systems—most notably “Vulcan,” a highly sensitive robot equipped with tactile capabilities. Utilizing force feedback sensors, Vulcan can discern the pressure or grip it exerts on objects, enabling it to determine whether its actions might damage the items being handled.
According to Aaron Parness, Director of Applied Science at Amazon, traditional robots have historically struggled to gauge whether the force applied to objects was excessive. With the integration of force feedback sensors, Vulcan is capable of detecting such nuances and employs artificial intelligence to learn and adapt the appropriate level of pressure required when handling various items.
Amazon further explained that Vulcan has been trained on vast datasets and refined through advanced algorithms to handle thousands of object types and logistical tasks. These include delicately transporting sensitive electronic equipment or picking up something as light as a pair of socks with just the right amount of force.
Vulcan is also designed to learn from its mistakes, meaning its performance will become increasingly precise over time as it gains experience determining optimal handling pressure for different items.
The deployment of Vulcan is part of Amazon’s broader initiative to enhance the efficiency of its picking operations while simultaneously improving workplace safety. For instance, Vulcan can assist in retrieving items stored at heights of up to eight feet (approximately 2.44 meters), thereby reducing the physical risks faced by human workers who would otherwise need to climb and reach. This not only mitigates potential injuries but also contributes to overall operational productivity.
Currently, Vulcan has been implemented in Amazon fulfillment centers in Spokane, Washington, and Hamburg, Germany.
In addition to Vulcan, Amazon has also introduced six other robotic systems across its logistics network. These include “Tipper,” which automates the unloading of goods from trucks and transfers them onto conveyor belts, and “Echelon,” a system designed to read and interpret item data as products move along conveyor systems.
Further innovations include “Agility” and “Matrix,” robots that assist with sorting goods, as well as “ZancaSort,” which delivers items and corresponding packaging materials directly to workers at ergonomically optimized heights, thereby enhancing the efficiency of the packing process.
Lastly, Amazon has unveiled “VASS,” a system that leverages computer vision and projection technology to intelligently sort goods into designated picking zones, streamlining the retrieval process for both human staff and robotic handlers.